Bevezetés
A celluláris anyagok napjainkban előtérbe kerültek. Elsősorban a műanyag habok terjedtek el: hungarocell, szivacsok, csomagolóanyagok, poliuretán habok stb. Azonban ezek alkalmazhatóságának többek között hőmérsékletfüggőségük és kis szilárdságuk szab határt. A fémből készült celluláris anyagok, a fémhabok éppen azért érdekesek, mert ezek a hátrányok nem jelentkeznek.
A fémhabokat szerkezetük alapján két csoportba oszthatjuk. A nyitott cellás fémhabok üregei egybefüggőek, vázukat egymáshoz kapcsolódó cellaélek alkotják. Míg a zárt cellás fémhabokban az üregeket cellafalak különítik el.
A fémhabok, amelyek néhány mikrométeres vagy akár centiméteres nagyságú üregeket is tartalmazhatnak (1. ábra), s amelyekben a cellák falvastagsága is igen széles skálán változhat (10-6–10-3 m) — szerkezetüket tekintve hasonlóak a műanyaghabokhoz. A fémhab sűrűsége lényegesen kisebb a tömör fémekéhez viszonyítva, átlagos sűrűségük a fém sűrűségének akár százada is lehet. A fémhabok egyik leggyakoribb jellemzője a relatív sűrűség, amely a fémhab sűrűségének és a fémhabot alkotó fém sűrűségének hányadosa. A jelenleg előállított fémhabok relatív sűrűsége 0,1% és 50% között változik.
Az alkalmazási területeiket mechanikai, elektromos, akusztikus, kémiai tulajdonságaik nagymértékben befolyásolják. Összenyomással, benyomással, ütéssel való alakításuk sajátos, lényegesen eltér a tömör fémeknél megszokottól. Merevek és jó alakítási, hővezetési tulajdonságokkal is rendelkeznek. Szilárdságuknál és lyukacsos szerkezetüknél fogva jó ütközésienergia-elnyelők, magashőmérsékleti és nagynyomású szűrők; akusztikus tulajdonságuk révén jó hangfogók, hangszigetelők.
Az ütközési energ ia elnyelését használják ki az autógyártásban és golyóálló mellények béléseként történő felhasználásuk során. Hővezetési képességük nem jó, ezért fémhabokat hőszigetelőként is használnak. Elektromos vezetőképességük is lényegesen kisebb a tömör fémekénél. Ütés- és tűzálló, illetve hőszigetelő tulajdonságuk miatt jól alkalmazhatóak veszélyes anyagok, vagy nagy értékű, érzékeny berendezések csomagolóanyagának gyártására. A járműipar a legelterjedtebb felhasználási területük, ahol könnyű szerkezeti és térelválasztó anyagokat, úgynevezett szendvicspaneleket készítenek belőlük.
A kutatások során felfedezett újabb tulajdonságaik egyre szélesebb körű alkalmazási lehetőségeket kínálnak. Felhasználják őket nagy fajlagos felületük miatt kémiai katalizátorok hordozóanyagaként, akkumulátorokban nagy felületű elektródaként. Robbanásveszélyes folyadékok tárolására szolgáló tartályok belső terét — a mozgatás során adódó nagy nyomásnövekedések elkerülése érdekében — szintén fémhabbal töltik ki. Az elektrotechnika is kezdi f elismerni ezen új anyagok jelentőségét. Nagyteljesítményű félvezető eszközöknél hőelvezetésre használnak speciálisan erre a célra készített, réz alapanyagú fémhabokat. Rendkívül jó hűtőteljesítményt sikerült elérni ezen a területen is. Méltán nevezi a Europhysics News egyik cikke a fémhabokat a XXI. század anyagának [1].
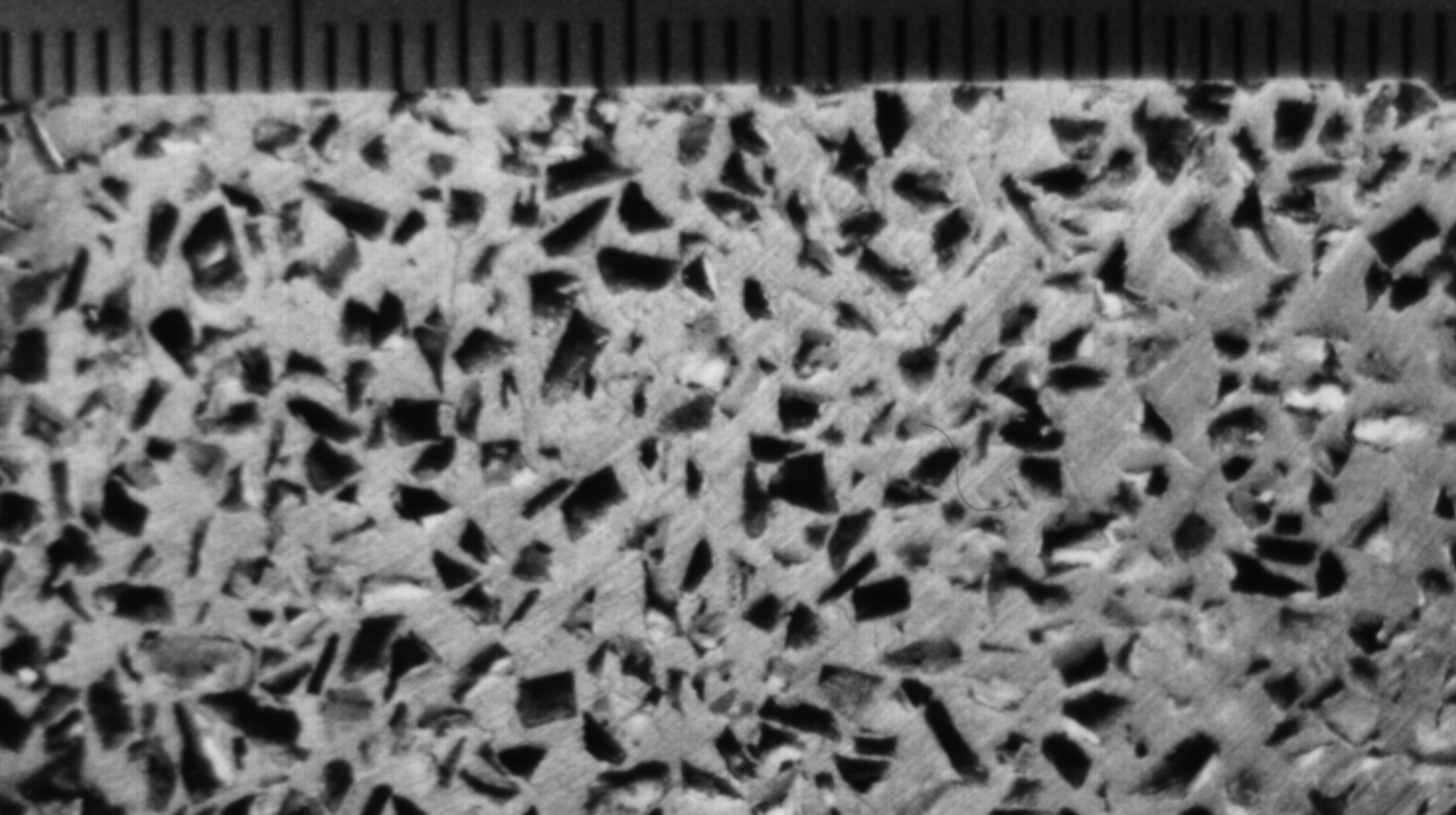
1. ábra
Nyitott cellás alumínium fémhab síkmetszete (Az ábra felső részén milliméterskála látható) [4]
A gázzal készült kompozitok, a fémhabok előállításával már az ötvenes években foglalkoztak, de a kezdeti sikertelen kísérletek után a kutatás abbamaradt. Később fejlettebb technológiával újra próbálkoztak. Folyamatos előállításuk és tudományos vizsgálatuk csak a hatvanas évektől kezdődött. Napjainkban számos módszer használatos fémhabok előállítására. Léteznek öntéssel, fémleválasztással, porkohászati eljárásokkal, fecskendezéses fémbevonással készülő fémhabok (2. ábra).
Fémhabok gyártása |
Öntés |
Fémmel való bevonás |
Porkohászat |
Fémmel való bevonás szóratással |
Az olvadék habosítása
Buborékoltatásos habosítás
Granulátumra öntés
Üreges gömbök egyesítése fémmel
Minta utáni öntés |
Polimer szálak fémmel való bevonása |
Öntőpépes habosítás
Lazapor-szinterelés
Üreges granulátum szinterelése
Szálkohászat
Öntőpéppel telített szivacs szinterelése
Pórusokba zárt gázzal habosítás
Szinterelési-kioldási eljárás |
Fémben oldott gázokkal történő habosítás |
2. ábra
Az eddig kidolgozott fémhabgyártási módszerek [3,4]
Ebben a cikkben a fent említett előállítási módszerek áttekintését tűztük ki célul [2,3,4]. Az egyes eljárásokat a teljesség igénye nélkül mutatjuk be.
Öntési eljárások
Zárt cellás fémhab előállítása habosítással
1948-ban A. Sosnik próbálkozott először higany alumíniumban való párologtatásával, hogy így habos alumíniumot kapjon. Az első alumíniumhabot azonban csak J. C. Elliottnak (1951) sikerült előállítani e technika továbbfejlesztésével.
Az első fémhab-előállítási kísérletek műanyagok habosítási technikájához hasonlítottak. Az olvadt fémhez gázfejlődés közben bomló, úgynevezett fúvatóanyagot (TiH 2-et illetve ZrH2-et) adagolnak. A keveréket a szemcsék bomláshőmérsékletére melegítve a felszabaduló gázok “buborékokat” alkotnak, melyek mozgása, egymáshoz illeszkedése alakítja ki a végső szerkezetet. E szerkezet szilárd állapota a fémhab. Ez a gyártási folyamat azonban nehezen szabályozható, és nem egységes cellaszerkezet alakul ki. Nagy gázbuborékok keletkeztek középen, míg a hűtött felületek (kokilla) közelében a sűrűség egyre növekedett. A nem kívánt nagyméretű buborékok és az inhomogén eloszlás leküzdésére számos megoldást vezettek be.
A buborékokat nagysebességű (10000 min -1 fordulat nagyságrendű) keveréssel 10 másodperc alatt egyenletesen el lehet oszlatni. Ekkor figyelték meg azt is, hogy minél egyenletesebb az eloszlás minden esetben, kivétel nélkül, annál jobb hab készül. A buborékok méretének, olvadt fémbeli eloszlásának (keverés) függvényében különböző porozitású fémhab állítható elő.
Fontos paraméter az olvadék viszkozitása, melynek növelésével biztosítható a szerkezet stabilitása. A buborékok mozgása ugyanis lelassul, a nagy viszkozitás a buborékok szökését jelentősen csökkenti. Az olvadék viszkozitása növelhető ötvözetek alkalmazásával vagy viszkozitásnövelő adalékkal. Viszkozitásnövelő például a salak, de használnak e célra gázokat vagy folyadékokat is, például levegőt, nitrogént, oxigént, szén-dioxidot, argont vagy vizet (L. M. Niebylski, C. P. Charema és T. E. Lee, 1974). Az így készült habokban kisebb üregméretek alakulnak ki, de a cellák mérete egyenletes.
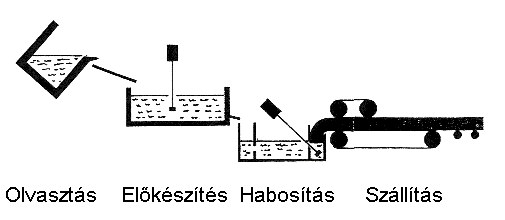
3. ábra
A habosítási eljárás e gyszerűsített vázlata folyadékállapotú alumíniumötvözet esetén [2]
Nehézség, hogy a habképző fúvatóadalékot az olvadékhoz adva viszonylag rövid idő múlva a habképződés megindul. Ezen a problémán az öntőedény megfelelő kialakításával segítettek, s azzal, hogy az olvadék az adalékkal való összekeverés után rövid időn belül az öntőformába kerüljön. A fémhidrid bomlása — és ezáltal a kialakuló cellák mérete — szabályozható. Alumínium fémhab előállításakor például a szemcsés fúvatóanyagot és az alumíniumot nagy arányban tartalmazó szemcsés anyagot összekeverik, majd felmelegítik. Ezután a keveréket 450 °C és 480 °C között legalább 5 percig tartva, a fémhidrid felületének oxidálásával szabályozható. Ezzel az előkészítéssel a fémhidrid bomlása szabályozhatóvá válik. A 3. ábra mutatja az előállítás egyszerűsített vázlatát.
Buborékoltatásos habosítás
Ez az eljárás az előző módszeren alapszik. Az olvadt fémen általában gázt buborékoltatnak keresztül (4. ábra), de víz befecskendezésével is képezhetünk buborékokat. A felületi feszültség csökkentésére — így a habosodás elősegítésére — habképző adalékot adnak az olvadékhoz. Ilyen adalékkal kevert anyag lehet például az Al-SiC, illetve az Al-Al 2O3. [5]
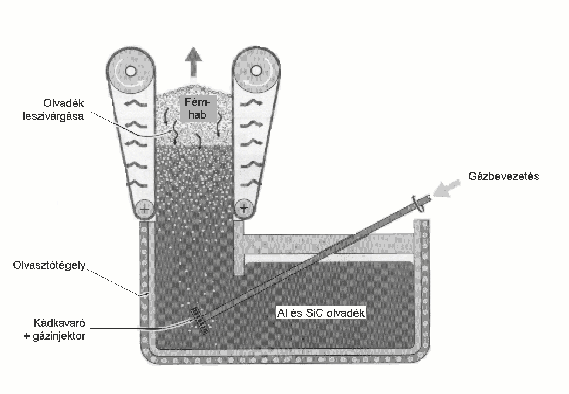
4. ábra
Gáz buborékoltatása az olvadékba [2]
Nyitott cellás fémhab előállítása granulátumok felhasználásával
A módszerhez a fém olvadáspontján stabil anyagból készült granulátumokat használnak. Ilyen anyag például a konyhasó, amely megszilárdulás után a fémből oldással eltávolítható. Magas hőmérsékleten a só porladhat, ezért a méret szerint válogatott sószemcséket először a majdani öntési hőmérsékleten ki kell hevíteni, majd újra kell szitálni.
Az öntőforma aljára helyezett előmelegített granulátumokra helyezett tömör fémet a lezárás után kemencében olvadáspontra melegítjük. A fém felületi feszültsége nagy, és jelentős viszkozitása is akadályozza a fém beáramlását a sószemcsék közötti üregekbe. A gyorsabb és hatékonyabb üregkitöltést az öntőforma fedőlapján keresztül bevezetett inert gázzal megvalósított túlnyomással segíthetj ük elő, vagy az öntőforma alján alkalmazott vákuumszívással. Alumíniumötvözetek esetén nitrogéngázt szoktak alkalmazni. Az öntőforma alján szellőzőlyukak találhatók, amelyek lehetővé teszik, hogy a fém lefelé áramlásakor a kiszorított gáz eltávozzon. Ezután hűtéssel juthatunk a só–fém kompozithoz, amely ebben az állapotban könnyen esztergálható, marható, darabolható. Fémhabot a só vízzel történő kioldásával nyerünk, így jutunk úgynevezett nyitott cellás fémhabhoz. A só kioldásához ajánlatos meleg folyóvizet alkalmazni, így lényegesen hamarabb kioldódik a só, mint áztatásos oldással (5. ábra).
Az eljárás előnye alacsony előállítási költsége, nagyméretű anyagok gyártásának lehetősége, az anyag könnyű forgácsolhatósága. A cellák alakja, mérete a granulátumok előkészítésével (szitálás, legömbölyítés) szabályozható. Lehetőleg egyenletes szemcsenagyságú granulátumot kell alkalmazni, ezzel viszonylag homogén felépítésű szerkezet biztosítható. Vízben oldódó sók helyett granulátumként használnak olyan anyagokat is, me lyek könnyen összenyomhatók, törhetők (például duzzasztott agyag, üveggyöngyök, üreges korundgömbök stb.). E módszerrel öntöttvas-, alumínium-, magnézium-, cink-, ón-, ólomfémhab állítható elő, összetett, bonyolult formák hozhatók létre.
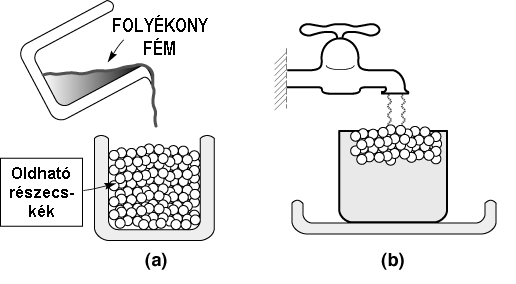
5. ábra
(a) Kiold ható granulátum (például só) réseinek kitöltése folyékony fémmel (például alumínium vagy ötvözetei)
(b) A részecskék kioldása a megfelelő oldószerrel (például vízzel) és nyitott cellás fémhab adódik [2]
Ennek egy különleges esete az az eljárás, amelynél ol yan üreges fémgömböket alkalmaznak a fémhab előállításához, mely szerves részévé válik a habnak. A szemcséket speciálisan készítik elő, például a fenoltartalmú műanyag ballonocskákat inert gázban melegítve kokszosítják, ezzel üreges széngömböcskéket hoznak létre. Ezekre fémet párologtatnak, majd a szén kiégetésével illeszkedő fémgömbökből felépített anyagot kapnak. A módszer kiválóan alkalmas hőálló, nehezen olvadó fémeszközök készítésére. E módszerrel például volfrámból 60-80 µm átmérőjű, egységesen 2 µm falvastagságú cellákat is sikerült készíteni.
Precíziós, minta utáni öntés
Japánban egyedülálló öntési technikát dolgoztak ki. Szivacsos szerkezetű műanyag hab üregeit folyékony hőálló anyaggal töltik meg (általában kerámiával), amit megszilárdítanak. Ezt az anyagegyüttest hőkezelve a műanyagot elpárologtatják. Az olvadt fémet ezután a műanyag hab helyére öntik, hagyják a fémet megszilárdulni, majd az “öntőformát” vegyi úton eltávolítják. Így a műanyag szivaccsal szinte azonos szerkezetű fémhab állítható elő. Az eljárás jól reprodukálható habokat eredményez. Ezt a technikát főként viszonylag alacsony olvadáspontú fémek esetében alkalmazzák, mint például alumínium, ólom, cink, ón, réz és ezek ötvözetei. Nyitott cellás habot kapnak, amelynek relatív sűrűsége 1 0 % körüli.
Fémhab gyártása fémbevonat készítésével
Ez a módszer poliuretán szálak fémmel való bevonására épül. Alapvetően három részből áll: megmerevítés, előzetes, nem elektrolitikus, fémmel való bevonás és végül elektrolitikus bevonás.
A megmerevítés lén yege, hogy a poliuretán habot vékony epoxy réteg felvitelével kellően merevvé teszik. Erre a gyártott fém alakjának megtartása miatt van szükség, mivel a poliuretán hab igen hajlékony. Ezután a poliuretán hab felszínét enyhén vezetővé teszik nem elektrolitikus bevonással. Ennek előkészítéséhez erősen oxidáló savval (króm-, kén-, foszforsav keverék) kell a felületet kezelni, amely a felületet vízzel nedvesíthetővé teszi, illetve mikroérdességet alakít ki rajta. Ezáltal növelik meg a későbbiekben rávitt fémréteg adhézióját. Ezután palládium-klorid oldatból kiváló palládiummal katalizálják a felületet. Ezt követően a nem elektrolitikus bevonóoldatba való merítéssel megkezdődik a folyamatos fémrávitel. A bevonófém lehet réz, nikkel, vas, ezüst, kobalt, arany és palládium. Ezen előkészítések után az előzetesen bevont uretán hab az elektrolitikus bevonás során a kívánt vastagságúra növelhető. Ehhez a bevonáshoz használt fém–elektrolitikus oldat általában réz–pyrofoszfát, nikkel–szulfamát, cink–cianid és ezüst–cianid.
Végül az uretán szubsztrát hőkezeléssel eltávolítható. Ezzel a módszerrel előállított habok kivételesen egységes szerkezetűek és porozitásuk nagyfokú, azonban magas előállítási költségük korlátozza alkalmazásukat. Az eljárással üreges cellaélekkel rendelkező nyitott cellás fémhab gyártható.
Porkohászati eljárások
Öntőpépes habosítás
Az öntőpépes habosítási eljárásnál egy iszapszerű anyagot készítenek finom fémporból és habképző anyagból, melyet egy szerves hordozóban oszlatnak szét. A keveréket felverik, majd kiégetik, ezzel szilárd porózus szerkezetet nyernek. Ezt a technikát berilliumporokra fejlesztették ki, majd alkalmazták más közönséges fémekre is, mint például nikkel, vas, réz, rozsdamentes acél és bronz. Alumínium esetén az öntőpépben alumínium port diszpergálnak szét, és habképzőnek sósavat, alumínium-hidroxidot vagy orthofoszforsavat használnak. Összekeverés után az anyagot a megfelelő öntőformába öntve a kívánt alakot veszi fel. A habosodás leülepedése után a habot hőkezelésnek vetik alá, hogy mechanikai tulajdonságait javítsák. Alumínium esetén nem alkalmaznak szinterelést a keletkező alumínium-oxid miatt. Ennélfogva ezek a habok viszonylag kis szilárdságúak, amely megszabja alkalmazhatóságukat.
Lazapor-szinterelés
Ennél az eljárásnál a fémport nyomás alkalmazása nélkül szinterelik. Ezt az eljárást használják porózus fémek, mint például bronzszűrők, porózus nikkel membránok (alkalikus akkumulátorok elektródáihoz és üzemanyagcellákhoz) gyártására. A lazapor-szintereléssel előállított anyag porozitása 40-től 60 térfogatszázalékig terjed.
Az anyag porozitásáak növelése érdekében kézenfekvőnek tűnik olyan helykitöltő adalékok hozzáadása, amelyek elbomlanak vagy elpárolognak a szinterelés alatt, vagy pedig szublimációval vagy feloldással eltávolítható. A vasból, rézből, nikkelből vagy ezek ötvözeteiből készült szűrők gyártása során ez a helykitöltő adalék gyakran ammónium-tetraklorid. Így nikkel membránok esetén 90 %-os porozitást is megvalósítható, amelyet 40 térfogatszázalék metil-cellulóz hozzáadá sával értek el.
Szinterelési-kioldási eljárás (SDP)
Két különböző eljárás, a szinterelés és a sóra öntés ötvözésével, Y. Y. Zhao és D. X. Sun új módszert dolgozott ki nyitott cellás fémhabok gyártására, amelyet SDP-nek (Sintering-Dissolution Process) neveztek el. Ennek során alumínium port konyhasóval kevernek össze a kívánt porozitásnak megfelelő arányban. A keveréket öntőformában összenyomják, majd szinterelik a fém olvadáspontja körüli hőmérsékleten. Ezután lehűtik a kompozitot szobahőmérsékletre. A habo t a só kioldásával kapjuk.
Tapasztalat szerint az így előállított fémhab relatív sűrűsége a só–fém-arány módosításával 15% és 50% között változtatható, míg a pórusok mérete és alakja a sószemcsék nagyságának és alakjának változtatásával befolyásolható. A módszernek három nagy előnye van: egyrészt a relatív sűrűség széles tartományon belül változtatható, másrészt a cellaméretek egyenletes eloszlásúak, harmadrészt formába öntéssel jelentős költségek takaríthatók meg az utómunkálatok szükségtelenné válásával. Azonban a módszernek hátránya is van, a só nem oldható ki teljes mértékben a fémhab belsejéből. [6]
Üreges granulátum szinterelése
Az eljárás nagyon hasonló a 2.3. részben tárgyalt előállítási módszerhez. Először üreges fémgömböcskéket gyártanak módosított porlasztási eljárással, illetve fémoxid vagy fémhidrid szinterelésével, majd színítésével (redukciójával). Réz, rozsdamentes acél és Ti-6%Al-4%V gömböcskéket állítanak elő ilyen módszerrel, majd ezeket az üreges golyócskákat szinterelik (6. ábra).
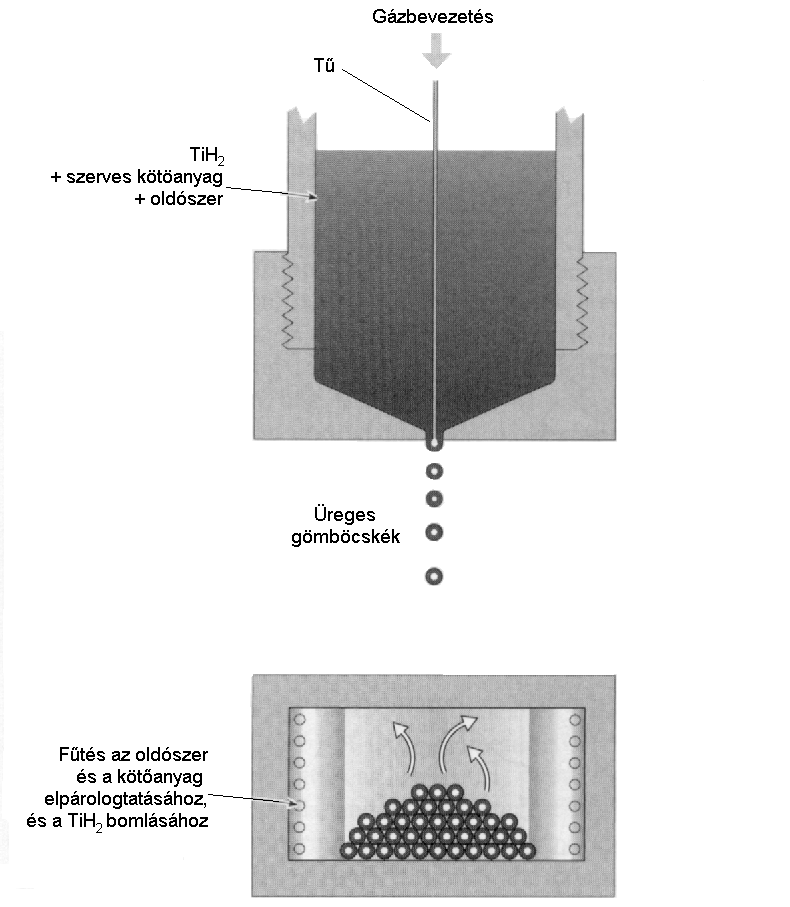
6. áb ra
Üreges gömböcskék előállítása és szinterelése [2]
Szálkohászat
Porózus anyagok — különösen szűrők — gyártásánál előnyös lehet fémpor helyett fémszálakat használni. Ennek az eljárásnak három jó tulajdonsága van. Egyrészt a porozitás széles tartományban szabályozható (0-95%). Másrészt nagy szilárdságú és nyújthatóságú anyag keletkezik a fémporral készült anyagokhoz képest, harmadrészt áteresztőképessége tervezhető.
Ezzel a technikával különböző fémekből gyártanak szűrőket, mint például rozsdamentes acél, réz, nikkel Ni–Cr-ötvözetek. Egyedülálló tulajdonságaik és a fémszálak gazdaságosabb előállítása miatt a porózus fémszálas anyagok iránt megnőtt az érdeklődés.
Öntőpéppel telített szivacs szinterelése
Egy szivacsszerű szerves anyagot (például természetes szivacsot vagy szintetikus műanyagszivacsot) a kívánt alakra vágnak, majd megtöltik vagy átitatják az adott fémport tartalmazó öntőpéppel, amelynek hordozóanyaga lehet víz vagy más szerves folyadék. A telített szivacsot kiszárítják, hogy eltávolítsák a hord ozóanyagot. Az így kapott száraz, telített szivacsot felmelegítik arra a hőmérsékletre, ahol a szerves szivacsszerű anyag elbomlik. A szervetlen maradványanyagot tovább melegítik a szinterelési hőmérsékletre, ahol az elbomlott szerves anyag eltávozik. Lehűtés után nagyporozitású nyitott cellás szerkezetet kapnak.
Az eljárás egy másik változatában fémvegyületet használnak fémpor helyett. A fémvegyület a bomlási hőmérsékletre való hevítéssel fémmé alakul; ezzel egyidejűleg a hordozószerkezet megsemmisül, kiég. A használt fémvegyület lehet például fém-tejsavsó vagy 2-hidroxikarboxilsav-só. Ezt az eljárást nagy porozitású (70%-90%) ezüstlemezek gyártására használják.
Pórusokba zárt gázzal történő habosítás
Az előzőekben említett módszerek kombinálásával fejleszte tték ki ezt az eljárást. Nagy nyomású inert gáz fémpor pórusaiban csapdába esik, ezért nagy nyomású gáztérbe helyezik a fémport. Utána ezt a fém-gáz keveréket lemezzé hengerlik, miközben a tömített lemezkamra anyaga tömör oldallapokat képez. A lemezt felhevítik, hogy a fémporrétegben lévő gáz kiterjedjen.
Ezzel a módszerrel egy szendvicsszerkezetet kapnak, melynek magja körülbelül 30 %-os porozitású. Jelenleg a legjobb minőségű és legjobb hajlítási merevségű paneleket ilyen szendvicspanelekből készítik, például a Boeing által kifejlesztett eljárásban titánötvözetből készült port, 3 MPa kezdeti nyomású argongáz jelenlétében préselnek össze.
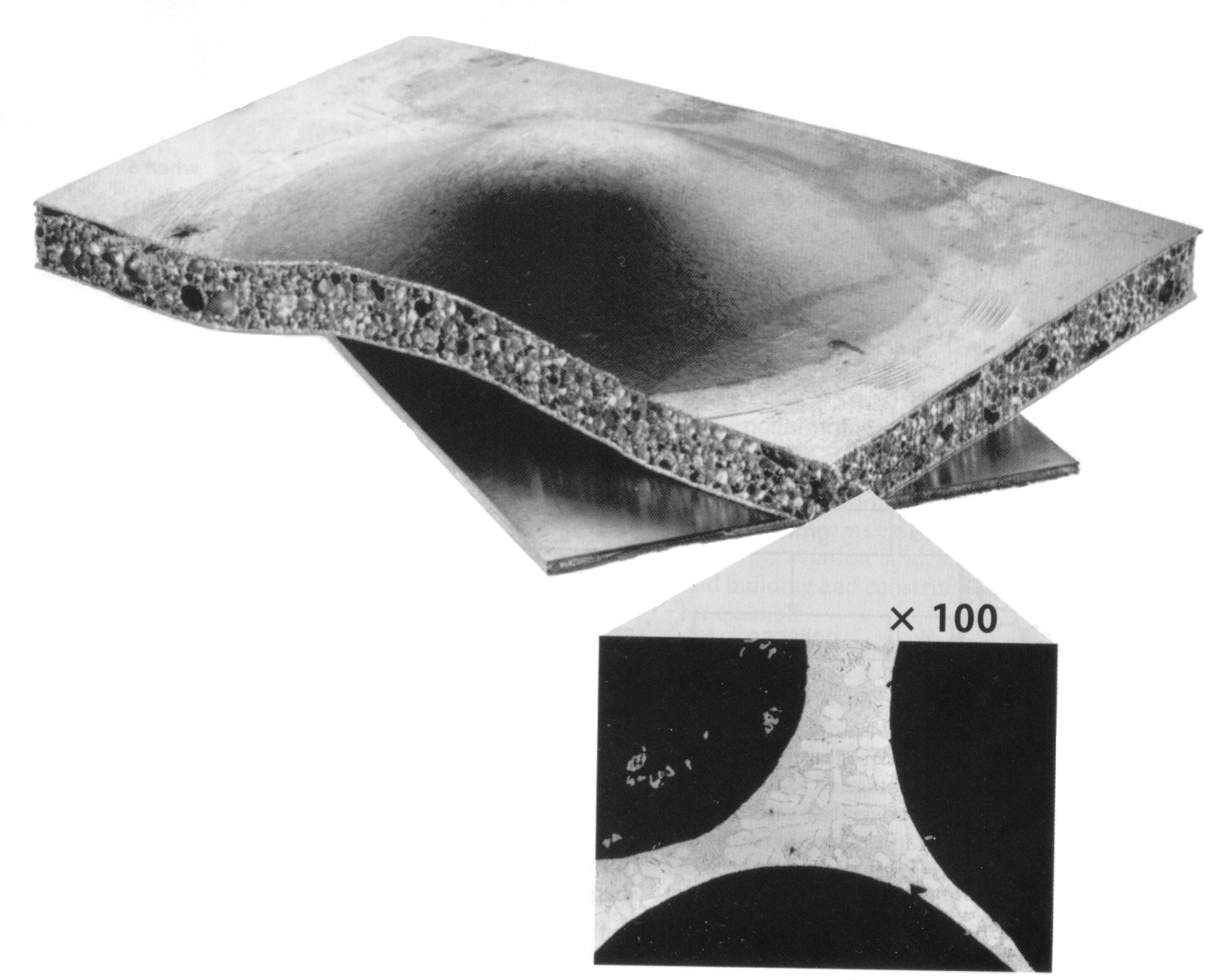
7. ábra
Szendvicspanel [1]
Fémmel való bevonás szóratással
Fémben oldott gázokkal történő habosítás
Az Egyesült Államokban kifejlesztett új módszer azt használja ki, hogy egyes fémek igen jól oldanak inert gázokat (pl. Pt és Pd jól old H2 gázt). A viszonylag magas gáztartalmú fémet egy szubsztrátra szóratják a gáz parciális nyomásán, így a gáz nem szabadul ki a fémből. Ezt követően felmelegítik a fémet az olvadáspontja fölé. Az ekkor felszabaduló és kiterjedő gáz buborékokat képez a fémben, így gázzal telt üregek keletkeznek. A fém lehűtése után zárt cellás szerkezet jön létre.
Ez a módszer a leghat ékonyabb jelenleg ismert eljárás inert gázt tartalmazó fémtest előállítására. Szóratóeszközként a triódás szórató berendezéseket részesítik előnyben, amelyben a plazma egy termikus elektronos (termionos) katód és egy anód között függetlenül képződik. A szubsztrát hűthető és a negatív rácselőfeszültség szabályozható. A szóratott fémben oldott inert gáz mennyisége a gáz nyomásával, a szubsztrát hőmérsékletével és a szubsztrátra kapcsolt negatív előfeszültséggel szabályozható.
Az oldott gáz mennyisége 15 és 23 00 ppm között változhat, az elérhető összes üregtérfogat pedig néhány százaléktól akár 80 %-ig is terjedhet. Ez az eljárás bármely olyan (akár nemfémes) anyagból történő hab-előállításhoz használható, amelyet katódporlasztással szóratni lehet, és inert gázt egyenletes eloszlásban tartalmaz.
Csak a főbb előállítási módszereket vázoltuk, a gyártástechnológiai részletek tárgyalásától eltekintettünk, a lehetőségek azonban korántsem kiaknázottak még.
Irodalom
J. Banhart: “Foam Metal: The Recipe”, Europhysics News 30 (1999) 17-20
M. F. Ashby, A. G. Evans, N. A. Fleck, L. J. Gibson, J. W. Hutchinson, H. N. G. Wadley: “Metal Foams: a Design Guide”, Butterworth–Heinemann, Boston (2000)
J. Davies, Shu Zhen: “Metallic foams: their production, properties and applications”, J. Mat. Sci., 18 (1983) 1899-1911
P. Kenesei: “Nagy relatív sűrűségű AlMgSi és AlSi fémhabok mechanikai és szerkezeti tulajdonságai”, Diplomamunka, ELTE TTK Ált. Fiz. Tsz. (2000)
O. Prakash, H. Sang, J. D. Embury: “Structure and properties of Al-SiC foam”, Materials Science and Engineering, A199 (1995) 195-203
Y. Y. Zhao, D. X. Sun: “A novel sintering-dissolution process for manufacturing Al foams”, Scripta mater. 44 (2001) 105-110
|